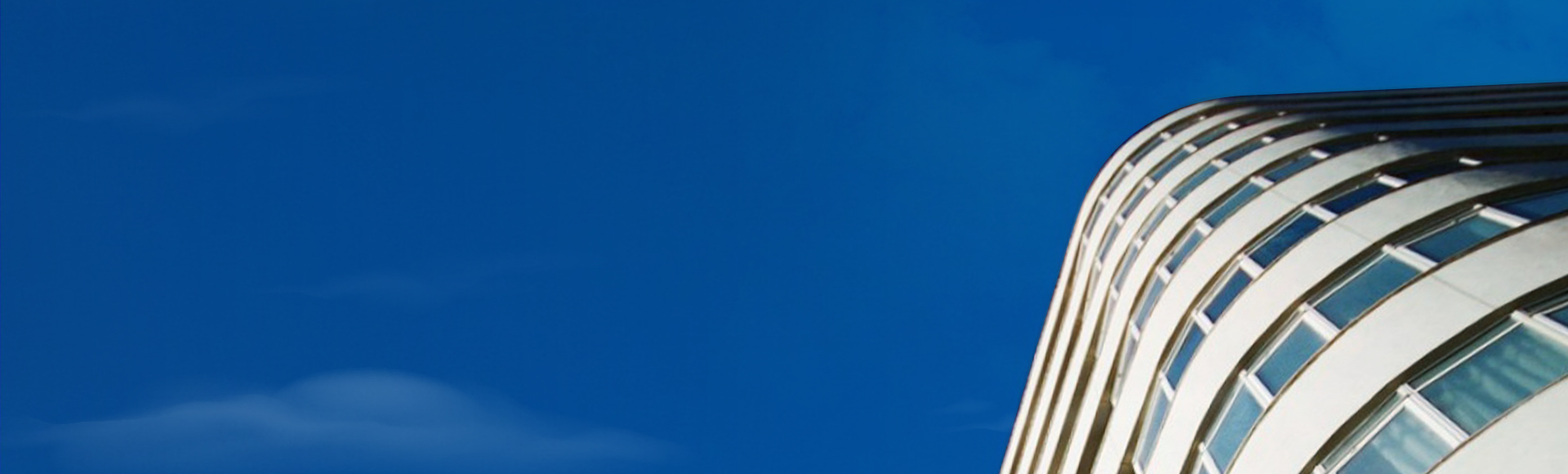
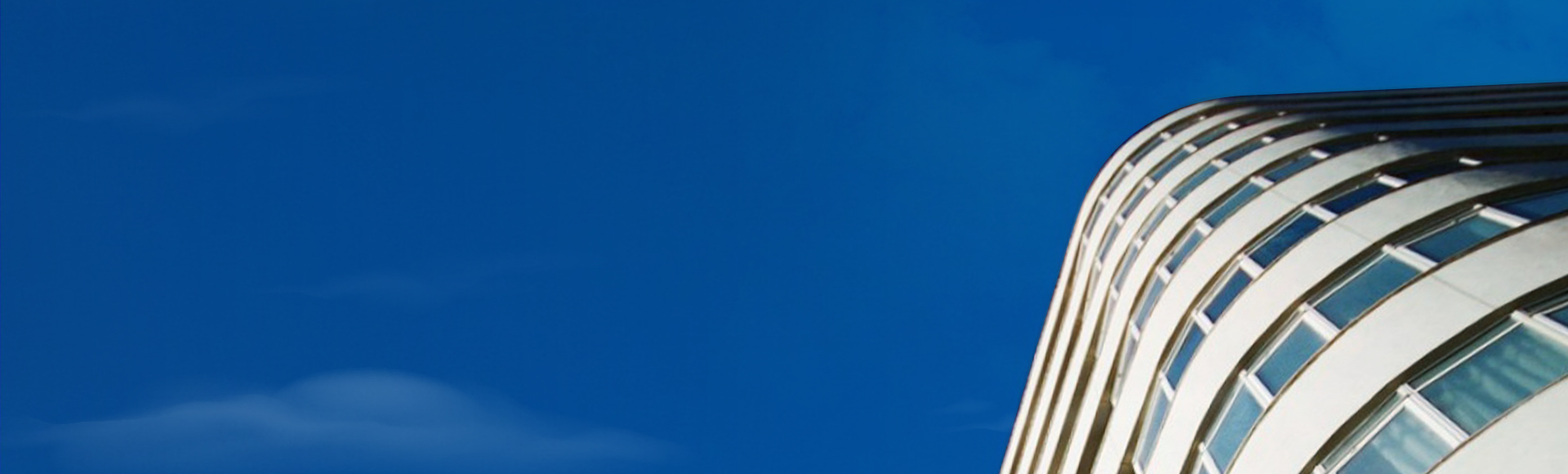
【2022 Annual Excellence Evaluation】Strive to create a learning oriented team, achieve high-quality and stable production, unite and move forward (Excellent Team Chapter)
As the production team at the end of the production chain, it is the foothold of the production line and a key link in ensuring product quality. Sintering Class 2 is a learning oriented team with a large proportion of new employees. Under the heavy workload of each master, they have to take care of two apprentices. On the premise of completing the tasks, taking care of the apprentices well can help them grow rapidly and become an indispensable part of them. In this reality, under the leadership of the class leader Xu Wenguang, the sintering team of Class 2 has united as one, made steady progress, and pursued practicality and innovation. They have repeatedly ranked first in the team's performance rankings and achieved good production results. We have completed the annual production task with high quality and quantity in 2022. The main team construction and management experience sharing is as follows:
1、 From the perspective of security management
The team has always closely integrated quality work with safety work, taking "systems always in place, alarm bells always ringing, and skills constantly practiced" as the employee safety production work concept, closely focusing on safety production, actively carrying out a series of team safety education and actions. Adhere to the principles of "four checks and four inspections" and "four implementations and one reporting", that is, to check ideological awareness and whether safety is given top priority; Check the homework environment to see if there are any safety hazards around you; Check the weak links and see if there are any staff members closely monitoring the scene; Check unsafe individuals to see if their awareness of independent security has been enhanced. The 'four implementations and one reporting' refers to the implementation of rectification measures, implementation of rectification time, implementation of rectification responsibilities, implementation of supervision and inspection personnel, and timely reporting of unresolved issues for identified unsafe problems. Safety is of utmost importance, and the feasibility and correction of emergency plans should be regularly reviewed to ensure safety hazards are not overlooked.
2、 From the perspective of product quality and stable production management
Firstly, strengthen on-the-job training. In the case of personnel shortage and a large number of new employees, a point-to-point, hands-on mentoring plan is adopted, with responsibility assigned to individuals and internal follow-up on the growth status of new employees to ensure the normal operation of production; Secondly, regular skill training should be conducted to ensure the implementation of the training mechanism. Regardless of how busy the work is, it is necessary to ensure regular monthly team job training activities, and require trainees to take careful study notes. The training content covers new requirements such as equipment, processes, products, and management, so that employees can understand them and, more importantly, understand their reasons, and improve their comprehensive work skills. Thirdly, in terms of on-site management, based on the 6s management theory of the workshop and combined with the actual situation of the company, detailed on-site management rules are refined, responsibility is assigned to individuals, and normalized management is carried out. Fourthly, for accidents that are prone to occur, revise them into files, improve and refine operating procedures, reduce accident rates and operational error rates, and better achieve various indicators.
3、 Always maintain a team atmosphere of unity and hard work
The working environment temperature of the sintering post is high, and due to seasonal reasons, the personnel turnover rate is relatively high, which fully tests the cohesion and centripetal force of a team. Based on this reason, the team has put more effort into cultivating team relationships. This team focuses on humanized management and emphasizes communication and interaction among team members. By holding regular team meetings to exchange work and share life, efforts are made to build the team like a small family, forming a team environment of enterprising optimism, mutual assistance and friendship, and sharing honor and disgrace, cultivating the spirit of respect and dedication among team members.