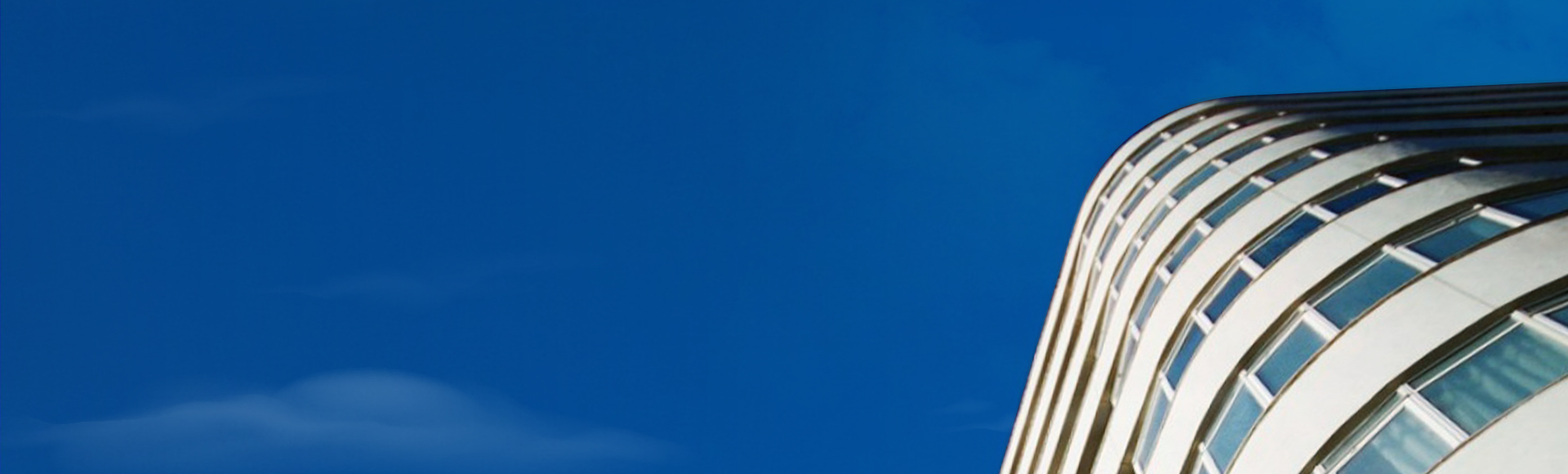
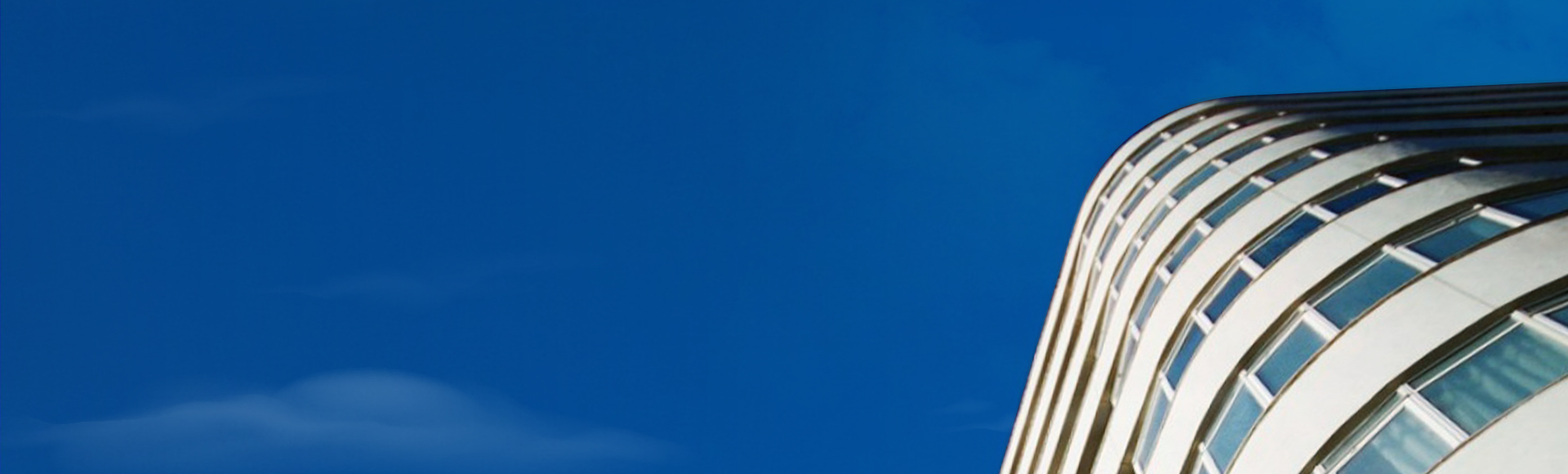
How can China's aviation composite industry chain achieve localization in the era of automation and digitization?
Composite materials are widely used in the aircraft industry, enabling engineers to overcome obstacles encountered when using materials alone. The constituent materials maintain their properties in composite materials, do not dissolve or completely fuse together in other ways. These materials together create a 'hybrid' material that improves structural performance.
The development of lightweight and high-temperature resistant composite materials will make the next generation of high-performance and economical aircraft designs a reality. The use of this material will reduce fuel consumption, improve efficiency, and lower the direct operating costs of the aircraft.
Composite materials can form various shapes, and if necessary, fibers can be tightly wrapped to increase strength. A useful characteristic of composite materials is that they can be layered, with fibers in each layer moving in different directions. This allows engineers to design structures with unique performance. For example, a structure can be designed to bend in one direction instead of bending in another direction.
Development stages of aviation composite materials
In 1970, composite materials were first applied to the aerospace industry, and their application range has developed from cabin doors, covers, fairings, etc. to now being applied to main load-bearing structures such as wings and fuselage; Meanwhile, with the continuous improvement of composite material technology such as carbon fiber, the use and substitution range of high-performance composite materials has further expanded, and the proportion of some aircraft composite materials has reached over 50%.
1. Civilian field
The application of composite materials in aircraft has gone through the process of applying main load-bearing structures such as leading edge, hood, fairing, spoiler, elevator, rudder, flaperon, vertical tail, flat tail, fuselage and wings. The application of composite materials has evolved from non load bearing components and secondary load bearing components of aircraft to main load bearing components, and is trending towards large-scale and integrated development.
The proportion of composite materials in China's civil aircraft is constantly increasing, from the initial 4% of Boeing 757/767 composite materials to over 50% of Boeing 787/Airbus A350 composite materials. The application of composite materials in aircraft manufacturing is constantly increasing.
2. Military field
Composite materials have their own unique contributions in improving aircraft body structure, reducing structural weight, and enhancing stealth capabilities, and are therefore widely used in fighter jets. Developed countries have applied composite materials to fighter jet manufacturing earlier. The actual proportion of carbon fiber used in the US F-22 is as high as 20%, and the proportion of composite materials used in the F-35 reaches 35%. Specifically, carbon fiber composite materials are widely used in the skin, wing structure, and body structural components. At present, the application of composite materials in China's fighter jets still needs to be improved. The proportion of composite materials used in the J-11B is about 12%, which is still a certain distance away from developed countries.
The number of civil and military aircraft in China is continuously increasing. According to statistics from the Ministry of Transport, as of 2021, the number of civil aircraft is 4054; According to the World Airforce 2022, as of 2021, China has a total of 3285 military aircraft, an increase of 25 from 2020. Under this trend, the use of composite materials in China's aerospace industry will continue to increase.
With the continuous upgrading of aircraft products in our country, requirements have also been put forward for composite materials used in aircraft, such as lightweight, wear-resistant, corrosion-resistant, low temperature resistant, high temperature resistant, and anti-oxidation. In the future, China's aerospace composite materials will develop towards high performance, low cost, and multifunctionality.
The 'automation' process is accelerating
With the increasing application proportion of composite materials and additive manufacturing in domestic civil aircraft, the manifestation in the "production end" is the introduction of more automation equipment. Taking the mass production of composite materials as an example, as the size and thickness of carbon fiber composite components continue to increase, the precision requirements for laying in the process are becoming higher and higher, and the laying is also done in different directions. In order to ensure quality and reduce human factors, the transition from manual tape laying to automatic tape/silk laying has become an inevitable trend in the industry.
Starting from this, subsequent processes such as the transportation, processing, and inspection of composite parts are also moving towards automation.
"Digitization is an industry trend"
Recently, at the 8th International Forum on Aerospace Materials and Manufacturing Technology (hereinafter referred to as the Aerospace Materials Forum), experts from companies such as Boeing and Siemens focused on the automation and digitization of the production and manufacturing process.
For example, the application of augmented reality (AR) technology in assembly, using artificial exoskeletons and other devices to assist manual operations and reduce work intensity, fully leveraging the advantages of manual and robot/automation equipment through human-computer interaction technology, improving production efficiency and reducing system failure rates through simulation of automation systems, building production standard processes through digital tools, quantitatively analyzing process simulation, simulation, and verification, and providing optimization suggestions.
The application of digitalization in the field of aviation materials is not only in these manufacturing stages, but also in the pre design stage, which cannot be separated from the assistance and empowerment of "digitalization".
Designers can enhance their understanding of new materials and processes through digital tools such as finite element analysis software, auxiliary design software, industrial software, etc., fully showcasing their advantages and disadvantages, thereby improving development speed, shortening development cycles, reducing development costs, and helping engineers find the optimal solution for structural design and material performance more efficiently.
Moving towards digitization also includes combining with emerging digital technologies such as big data, AI, and machine learning in recent years. For example, in the face of massive amounts of data generated during simulation work and experimental processes, digital technology can be used to help technicians efficiently organize and analyze the data.
Not only that, the "digitalization" sweeping the aviation manufacturing industry is constantly expanding from design, manufacturing and other stages. For example, in the airworthiness certification stage that concerns the success or failure of a type of aviation product, foreign countries are currently shifting their airworthiness certification thinking from the traditional "one configuration, one inspection" approach to simulation and analysis methods under digital tools. With the continuous extension of this "digitalization" path, it is gradually connecting and integrating the entire chain of design, manufacturing, assembly, testing, airworthiness certification, maintenance, modification and upgrading, forming "integration".
The 'Industrial Era' of Domestic Aerospace Composite Materials
Through the reports and speeches of experts on the forum, we have learned that the application of domestic civil aircraft in composite and additive manufacturing has taken the first step, for example, the proportion of composite application on C919 has reached 12%. But another fact behind the numbers is that the raw materials for these composite materials still come from abroad. So, in the future CR929, COMAC stated that while using imported raw materials, it will also use domestically produced materials, "incorporating domestically produced materials into the entire development process".
However, compared to the annual production of tens of thousands of tons of aviation composite materials in foreign countries, China's aviation composite material production scale is relatively small and has not yet entered the stage of large-scale industrial production. Regarding this, relevant experts attending the meeting emphasized that process performance and PCD documents ("material production process control documents") are the key to whether domestic aviation composite materials can pass the industrial batch production stage. Otherwise, it will lead to poor quality stability (manifested as significant fluctuations in the composition or performance of different batches of materials, high scrap rates, low production efficiency, increased processing costs, and even inability to install and apply). Experts have pointed out that "some domestic aviation materials have been approved, but PCD preparation is insufficient or promotion is not good, resulting in poor product stability".
It can be seen that the success of an aviation composite material is not only due to its excellent performance parameters and certification approval in the laboratory stage, but also depends on its "process performance" and whether it can have stable quality in various batches after entering the mass industrial production stage, while also considering production efficiency, production costs, etc.
Building a composite materials industry chain
For China's aviation manufacturing industry, the goal in the field of aviation materials is not only to achieve large-scale industrial production of domestically produced aviation composite materials, but also to "build a composite material industry chain" and cultivate core suppliers for the entire industry chain, including material suppliers, raw material suppliers, and process material suppliers. Their materials should cover the main material specifications, continuously meet quality standards and stability, strictly follow certification standards, and have international competitiveness.
These materials include not only T300 grade carbon fiber, T800 grade carbon fiber, glass fiber, and other composite core materials, but also the process materials and auxiliary materials required in the composite manufacturing process.
In addition, there is a particularly important link in this industry chain - equipment suppliers, including production equipment, laying equipment, molding equipment, processing equipment, testing equipment, etc. At present, the key domestic equipment is undergoing a transformation from "solving whether there is or not" to "usability", which is also a process of close collaboration, "two-way rush", and continuous iteration between manufacturers and domestic equipment suppliers.
Looking ahead to the future, with the continuous improvement of domestic equipment and the increasing production and wider use of domestic aviation composite materials, it will bring performance and economic advantages to domestic military and civilian aircraft.
How to achieve 'localization'?
But this path of "localization" is by no means an easy one. We must face the obstacles ahead, break through the technical fog, constantly overcome difficulties and challenges, and constantly move forward to make new breakthroughs.
This includes not only the significant gap in the application of composite and additive manufacturing in China's civil aircraft compared to Boeing and Airbus, but also the gaps and shortcomings in basic theory, key process technology, high-end equipment, core components, commercial software, and industrial applications when benchmarking against first-class technology.
And such a path will be a continuous pursuit of self-improvement, constantly moving forward and expanding boundaries. We need to continuously enhance our understanding of materials, recognize their characteristics and shortcomings, constantly tap into their performance potential, and establish a series of specifications, guidelines, requirements, standards, and systems that are compatible with them.
Especially compared to the relatively comprehensive understanding of the characteristics, processes, and defects of traditional aviation materials such as aluminum and titanium in the industry, there are still too many unknowns and mysteries about composite materials and additive manufacturing both domestically and internationally, which require a large amount of basic research and further scientific research to "grasp its defects". Only by doing so can we maximize the powerful driving force of the new generation of aviation materials and manufacturing processes on aviation technology.
Looking ahead to the future of aviation materials and manufacturing technology in China, it is a necessary path for the transformation and upgrading of China's aviation manufacturing industry to catch up, surpass, explore, and innovate. Although the road ahead is long and obstructed, the road ahead is approaching; if the road ahead is long and obstructed, the future is promising
Source: Xianji.com
Keywords: # alumina fiber # Dongheng national fiber # alumina continuous fiber # alumina fiber felt # alumina fiber felt # alumina fiber paper # refractory material # insulation material