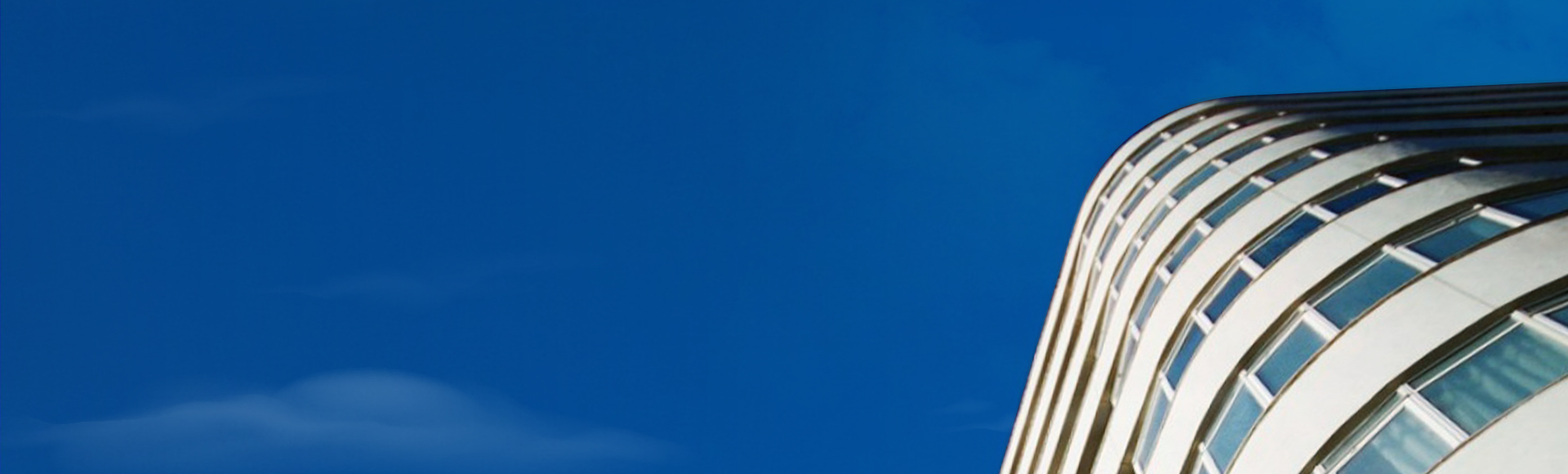
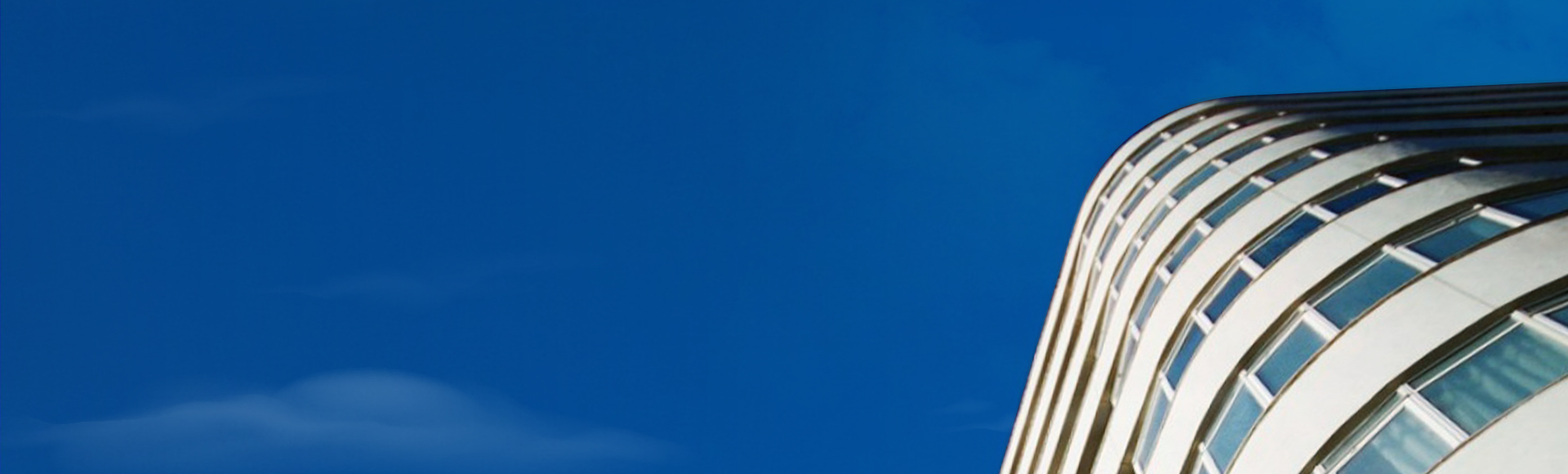
【Aluminum oxide fiber manufacturer】Overview of New Metal Matrix Composite Materials
01 Performance of Metal Matrix Composite Materials
Compared with traditional metal materials, MMC has higher specific strength, specific stiffness, and wear resistance; Compared with resin based composite materials, MMC has excellent electrical and thermal conductivity, good high-temperature performance, and weldability; Compared with ceramic based composite materials, MMC has the characteristics of high toughness, high impact performance, and low coefficient of linear expansion. Practical MMC should exhibit low density and mechanical properties comparable to current engineering materials.
The excellent performance of metal based composite materials is multifaceted, and the reinforcement greatly improves the yield strength and tensile strength of MMC. MMC has good high-temperature performance, such as high creep resistance. This is particularly prominent in long fiber reinforced MMC. After adding different reinforcements to the metal matrix, the wear resistance of the material is greatly improved, and the wear rate can be reduced by an order of magnitude. The density of the reinforcement added by MMC is low, so the density of the material can be significantly reduced. By utilizing the coefficient of linear expansion of ceramics as a reinforcing material, it can be used to adjust the coefficient of linear expansion of MMC, thereby obtaining composite materials that match various materials.
The performance of metal based composite materials is not only related to the composition, morphology, volume fraction, and matrix alloy composition of the reinforcing material, but also closely related to the interface microstructure, which is related to the preparation process, reinforcement surface treatment process, etc. According to different reinforcement principles, metal matrix composites can be divided into two categories: continuous fiber reinforcement and discontinuous reinforcement.
1. Long fiber reinforced metal matrix composite material
In continuously reinforced metal matrix composites, the reinforcing fibers mainly include boron fibers, carbon fibers (graphite fibers), SiC fibers, Al2O3 fibers, etc., and the matrix mainly includes aluminum, magnesium, titanium, copper, nickel, and their alloys. The properties of several typical continuous reinforced metal matrix composites are shown in Table 2. It can be seen that the performance of fiber-reinforced composite materials has anisotropy, with longitudinal direction significantly higher than transverse direction; The longitudinal strength and modulus of composite materials are significantly higher than those of the matrix alloy. In addition, many studies have shown that the fatigue resistance of continuous fiber-reinforced metal matrix composites subjected to tensile loads along the fiber direction (longitudinal) is superior to that of unreinforced matrix alloys, resulting in a general doubling of the fatigue limit. The creep resistance of alloys can often be greatly improved by the addition of continuous fibers. A typical example in this regard is the application of silicon carbide continuous fiber reinforced titanium based composite materials in aviation turbine engines to compensate for the low creep resistance of titanium alloys. Due to the addition of low expansion fibers, the coefficient of linear expansion of composite materials is significantly reduced. A typical example is the application of Gr/Mg in the support pole of the Hubble Space Telescope antenna, which maintains dimensional stability under repeated exposure to sunlight.
2 Short Fiber Reinforced Metal Matrix Composite Materials
The reinforcement effect of short fibers is between that of particles and continuous fibers. Due to the significantly lower performance and larger size of short fibers compared to whiskers, the reinforcement effect of short fibers is not as good as that of whiskers. The preparation methods of short fiber reinforced metal matrix composites mainly include powder metallurgy, pressure infiltration, extrusion casting, etc.
Short fiber reinforced aluminum matrix composites are currently the most extensively studied. The room temperature tensile strength of alumina short fiber reinforced aluminum matrix composites is not significantly improved compared to the matrix alloy (Table 3), but their high-temperature strength retention rate is significantly better than that of the matrix. The elastic modulus is greatly improved at both room temperature and high temperature, and the thermal expansion coefficient is reduced (Table 4). The wear resistance is improved.
In addition, the Al2O3 short fiber reinforced zinc based composite material prepared by squeeze casting method has a significant strengthening effect, and its high-temperature mechanical properties and wear resistance have been significantly improved. The performance of unreinforced magnesium alloys significantly decreases above 100-150 ℃, while the addition of reinforcements can significantly improve the high-temperature performance of the matrix alloy.
3 Whisker Reinforced Metal Matrix Composite Materials
The earliest experiment to use whisker reinforced metals was Al2O3 whiskers, but due to its high cost and difficulty in achieving uniform distribution of whiskers in the metal matrix, its development was not fast. However, the addition of inexpensive SiC whiskers significantly improved the elastic modulus and strength of the composite material, leading to the development of whisker reinforced metal research. The main matrix used for reinforcement is Al, Mg, and their alloys.
① Whisker reinforced aluminum based composite materials
The properties of SiCw/Al composite materials are shown in Tables 6 and 7. The relationship between the strength of SiCw/Al composite materials and the volume fraction of SiCw is shown in Figure 6. The relationship between the strength, elastic modulus, and temperature of SiCw/2024Al composite materials is shown in Figures 7 and 8. It can be seen that compared with the matrix alloy, the strength and modulus of the composite material have been significantly improved, and the high-temperature performance is excellent, but the density has slightly increased. The strength of composite materials increases with the increase of the volume fraction of whiskers, and their properties are also closely related to the preparation process and parameters.
② Whisker reinforced magnesium based composite materials
The properties of SiCw/Mg composite materials are shown in Table 8. Compared to the base alloy. The tensile strength, yield strength, and elastic modulus of SiCw/Mg composite materials are greatly improved, resulting in higher specific strength and modulus of the composite material.
02 Characteristics of Metal Matrix Composite Materials
The performance of metal based composite materials depends on the characteristics, content, distribution, etc. of the selected metal or alloy matrix and reinforcement. By optimizing the combination, not only can the good thermal and electrical conductivity, harsh environmental resistance, impact resistance, fatigue resistance, and fracture resistance of the base metal or alloy be obtained, but it can also have high strength, high stiffness, excellent wear resistance, and lower coefficient of thermal expansion (CTE). The characteristics of metal based composite materials are summarized as follows.
1. High specific strength, high specific modulus
Due to the addition of an appropriate amount of high-strength, high modulus, low-density fibers, whiskers, particles and other reinforcements in the metal matrix, the specific strength and modulus of the composite material have been significantly improved, especially with high-performance continuous fibers such as boron fibers, carbon (graphite) fibers, and silicon carbide fibers, which have high strength and modulus. The highest strength of carbon fiber with a density of only 1.85g/cm3 can reach 7000MPa, which is more than 10 times higher than the strength of aluminum alloy. The modulus of graphite fiber is 230-830GPa. The density of boron fiber is 2.4-2.6g/cm3, the strength is 2300-8000MPa, and the modulus is 350-450GPa. The density of silicon carbide fibers is 2.5-3.4g/cm3, the strength is 3000-4500MPa, and the modulus is 350-450GPa. Adding 30% -50% high-performance fibers as the main carrier of the composite material, the specific strength and modulus of the composite material are exponentially higher than those of the matrix alloy. Figure 2 shows a comparison of the properties between typical metal based composite materials and matrix alloys. Components made of high specific strength and high specific modulus composite materials are lightweight, rigid, and high-strength, making them ideal structural materials in the fields of aerospace and aviation technology.
2. Small thermal expansion coefficient and good dimensional stability
The reinforcing materials used in metal matrix composites, such as carbon fibers, silicon carbide fibers, whiskers, particles, boron fibers, etc., have both a small coefficient of thermal expansion and a high modulus, especially high modulus and ultra-high modulus graphite fibers, which have a negative coefficient of thermal expansion. Adding a considerable amount of reinforcement not only significantly improves the strength and modulus of the material, but also significantly reduces its thermal expansion coefficient. By adjusting the content of reinforcement, different thermal expansion coefficients can be obtained to meet various working conditions. For example, in graphite fiber reinforced magnesium based composite materials, when the volume fraction of graphite fibers reaches 48%, the thermal expansion coefficient of the composite material is zero, which means that parts made of this composite material do not undergo thermal deformation under temperature changes, which is particularly important for artificial satellite components. By selecting different matrix metals and reinforcements and compounding them together in a certain proportion, metal based composite materials with good thermal conductivity, low thermal expansion coefficient, and good dimensional stability can be obtained. Figure 3 shows the dimensional stability and specific modulus of some typical metal matrix composites and metal materials. It can be seen that graphite/magnesium composite materials have the highest dimensional stability and the highest specific modulus.
3. Excellent high-temperature performance
Due to the much higher high-temperature performance of metal matrix compared to polymers, reinforcing fibers, whiskers, and particles all have high high-temperature strength and modulus at high temperatures. Therefore, metal matrix composites have higher high-temperature performance than base metals, especially continuous fiber-reinforced metal matrix composites. Fibers play the main load-bearing role in composite materials, and their strength does not decrease significantly at high temperatures. They can be maintained close to the melting point of metals and have much higher high-temperature performance than metal matrices. Like tungsten wire reinforced heat-resistant alloy, its high-temperature endurance strength at 1100 ℃ for 100 hours is 207MPa, while the high-temperature endurance strength of the base alloy is only 48MPa; For example, graphite fiber reinforced aluminum matrix composite materials still have a high temperature strength of 600MPa at 500 ℃, while the strength of aluminum matrix has decreased to below 100MPa at 300 ℃. Therefore, metal based composite materials are selected for high-temperature components such as engines, which can significantly improve the performance and efficiency of the engine. In short, components made of metal based composite materials can be used at higher temperature conditions than those made of metal materials or polymer based composite materials.
Keywords: # alumina fiber # Dongheng national fiber # alumina continuous fiber # alumina fiber felt # alumina fiber felt # alumina fiber paper # refractory material # insulation material