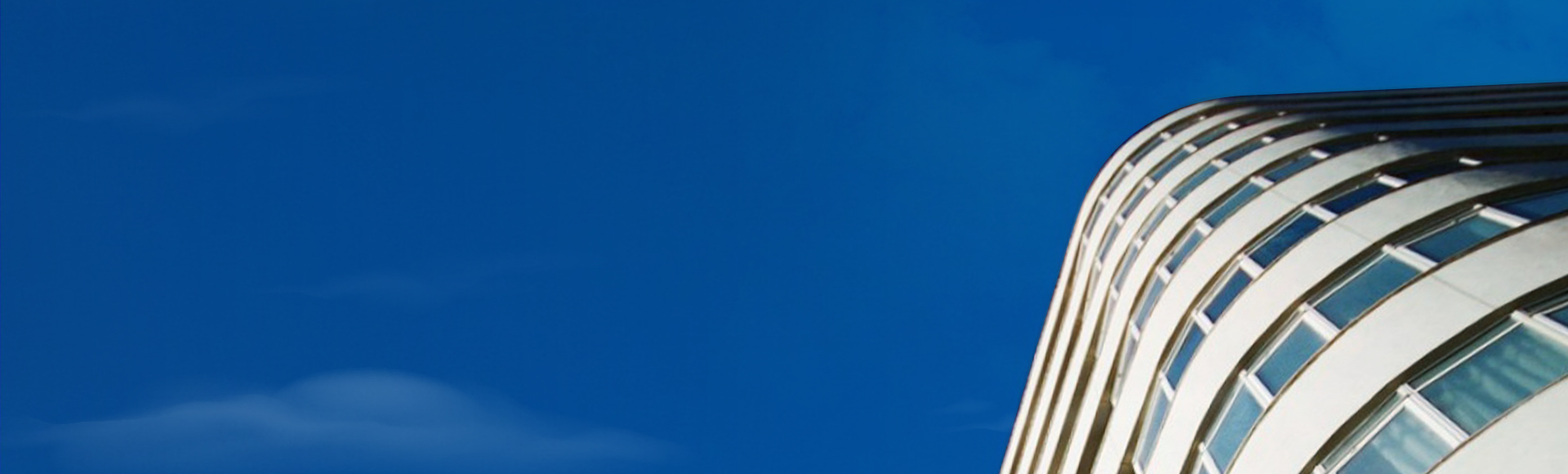
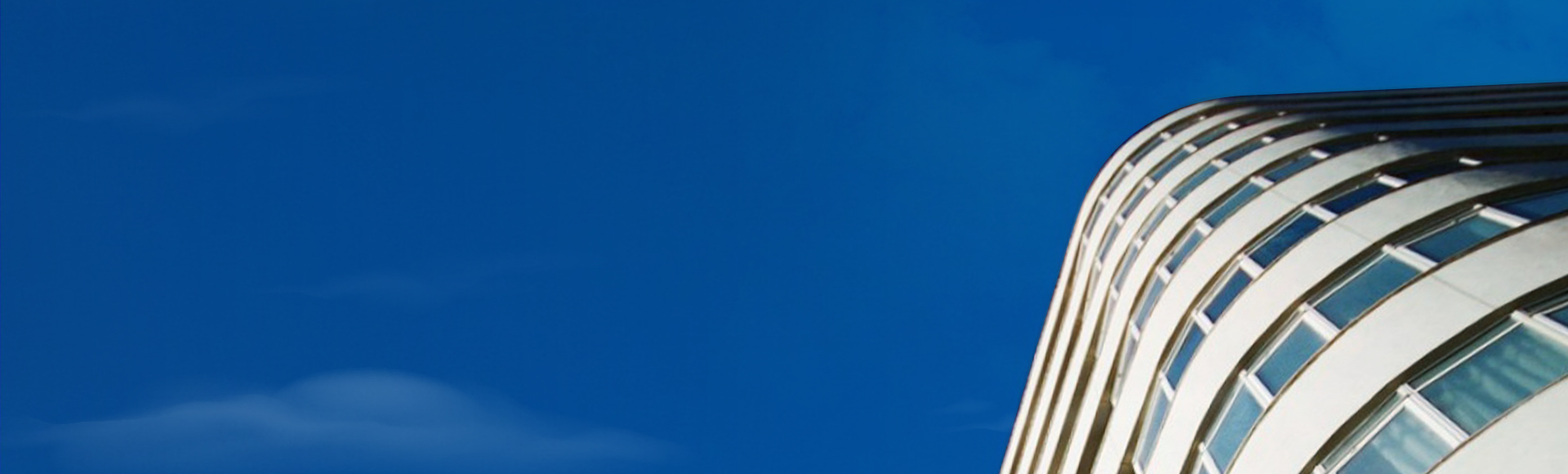
【Aluminum oxide fiber manufacturer】What are the key new materials for aircraft engines?
Aviation manufacturing is the most concentrated field of high-tech in the manufacturing industry and belongs to advanced manufacturing technology. The F119 engine developed by HP in the United States, the F120 engine developed by General Electric, the M88-2 engine developed by SNECMA in France, and the EJ200 engine jointly developed by the United Kingdom, Germany, Italy, and Spain. These high-performance aircraft engines, representing the world's advanced level, share the common feature of widely adopting new materials, processes, and technologies. Today, let's take a look at the new materials used in high-performance aircraft engines.
01 High temperature alloy
High temperature alloys are developed to meet the stringent material requirements of jet engines and have become an irreplaceable key material for the hot end components of military and civilian gas turbine engines. At present, the proportion of high-temperature alloys used in advanced aircraft engines has reached over 50%.
The development of high-temperature alloys is closely related to the technological progress of aviation engines, especially the materials and manufacturing processes of the hot end components such as turbine disks and blades, which are important indicators of engine development. Due to the high requirements for the high temperature resistance and stress bearing capacity of materials, the early UK developed Ni3 (Al, Ti) reinforced Nimonic80 alloy for use as turbine blade materials in turbojet engines, and subsequently developed the Nimonic series of alloys. The United States has developed dispersion strengthened nickel based alloys containing aluminum and titanium, such as Inconel, Mar-M, and Udmit alloy series developed by Pratt&Whitney, GE, and Special Metals, respectively.
In the development process of high-temperature alloys, manufacturing processes play a significant role in promoting the development of alloys. Due to the emergence of vacuum melting technology, the removal of harmful impurities and gases in alloys, especially the precise control of alloy composition, has continuously improved the performance of high-temperature alloys. Subsequently, the successful research on new processes such as directional solidification, single crystal growth, powder metallurgy, mechanical alloying, ceramic cores, ceramic filtration, and isothermal forging has promoted the rapid development of high-temperature alloys. Among them, directional solidification technology is the most prominent, and the directional and single crystal alloys produced by directional solidification process have a usage temperature close to 90% of the initial melting point. Therefore, currently, advanced aircraft engine blades in various countries are manufactured using directional and single crystal alloys for turbine blades. From an international perspective, nickel based cast high-temperature alloys have formed equiaxed crystals, directionally solidified columnar crystals, and single crystal alloy systems. Powder high-temperature alloys have also developed from the first generation 650 ℃ to 750 ℃, 850 ℃ powder turbine discs, and dual performance powder discs for advanced high-performance engines.
The development of high-temperature alloys in China has been driven by the demand for research and production of aviation engines. The entrepreneurship and development of high-temperature alloys in China began before the 1970s. Due to the demand for the first and second generation engines in China, the GH series of deformed high-temperature alloys and the K series of cast high-temperature alloys were developed. At the same time, many new manufacturing technologies were developed, such as vacuum melting and casting, hollow blade casting, isothermal forging, etc.
After the 1970s, in the development of high-temperature alloys, China introduced European and American technology, developed and produced according to foreign technical standards, and put forward higher requirements for the purity and comprehensive performance of materials. High performance deformed high-temperature alloys and cast high-temperature alloys were developed. Especially the research and development of DZ series directional solidification columnar crystal alloys and DD series single crystal alloys have taken China's high-temperature alloys to a new level in production process technology and product quality control.
02 Ceramic based composite materials
When it comes to ceramics, people naturally think that their characteristic is brittleness. More than a decade ago, it was impossible for anyone to accept using it as a load-bearing component in the engineering field. Even now, when it comes to ceramic composite materials, there may still be some people who are unclear, thinking that ceramics and metals were originally two unrelated basic materials. However, since people ingeniously combined ceramics and metals, their concept of this material has fundamentally changed, and this is ceramic based composite materials.
Ceramic based composite materials are a promising new type of structural material in the aviation industry, especially in the manufacturing and application of aircraft engines, where they are increasingly demonstrating their uniqueness. Ceramic based composite materials not only have the advantages of light weight and high hardness, but also have excellent high temperature resistance and high temperature corrosion resistance. At present, ceramic based composite materials have surpassed metal heat-resistant materials in withstanding high temperatures, and have excellent mechanical properties and chemical stability, making them ideal materials for high-performance turbine engines in the high-temperature zone.
At present, countries around the world are focusing on researching silicon nitride and silicon carbide reinforced ceramic materials to meet the material requirements of the next generation of advanced engines, and have made significant progress. Some have already begun to be applied in modern aviation engines. For example, the F120 engine of the American verification aircraft uses ceramic materials for its high-pressure turbine sealing device and some high-temperature parts of the combustion chamber. The combustion chamber and nozzle of the M88-2 engine in France also use ceramic based composite materials.
03 Intermetallic compounds
The development of high-performance, high thrust to weight ratio aircraft engines has promoted the development and application of intermetallic compounds. Nowadays, intermetallic compounds have developed into a variety of families, generally composed of binary, ternary, or multi-element metal elements. Intermetallic compounds have great potential in high-temperature structural applications. They have high operating temperatures, specific strength, thermal conductivity, especially at high temperatures. They also have good oxidation resistance, high corrosiveness, and high creep strength. In addition, as intermetallic compounds are a new material between high-temperature alloys and ceramic materials, they fill the gap between these two materials and become one of the ideal materials for high-temperature components of aircraft engines.
At present, the main focus of research and development in aircraft engine structures is on intermetallic compounds such as titanium aluminum and nickel aluminum. These titanium aluminum compounds have a density similar to that of titanium, but they have a higher operating temperature. For example, the operating temperatures for TiAl and TiAl are 816 ℃ and 982 ℃, respectively. Intermetallic compounds have strong interatomic bonding forces and complex crystal structures, making them difficult to deform and exhibiting hard and brittle characteristics at room temperature. After years of experimental research, a new type of alloy with high temperature strength, room temperature plasticity and toughness has been successfully developed and installed for use, with good results. For example, the high-performance F119 engine in the United States uses intermetallic compounds for its casing and turbine discs, while the F120 engine's compressor blades and discs use new titanium aluminum intermetallic compounds.
04 Ultra high strength steel
Ultra high strength steel is used as landing gear material in aircraft. The landing gear material used in the second generation aircraft is 30CrMnSiNi2A steel with a tensile strength of 1700MPa. This type of landing gear has a shorter lifespan, approximately 2000 flight hours.
The design of third-generation fighter jets requires the landing gear to have a lifespan of over 5000 flight hours. At the same time, due to the increase in onboard equipment, the weight coefficient of the aircraft structure decreases, which puts higher demands on the selection of landing gear materials and manufacturing technology. The third-generation fighter jets of both the United States and China adopt the manufacturing technology of 300M steel (tensile strength 1950 MPa) landing gear.
It should be pointed out that the improvement of material application technology is also driving the further extension of landing gear life and the expansion of adaptability. The landing gear of the Airbus A380 aircraft adopts ultra large integral forging technology, new atmosphere protection heat treatment technology, and high-speed flame spraying technology, which ensures that the service life of the landing gear meets the design requirements. As a result, the advancement of new materials and manufacturing technologies ensures the upgrading of aircraft.
The long-life design of aircraft in corrosion-resistant environments places higher demands on materials. Compared to 300M steel, AerMet100 steel has equivalent strength levels, while its general corrosion resistance and stress corrosion resistance are significantly better than 300M steel. The corresponding landing gear manufacturing technology has been applied to advanced aircraft such as F/A-18E/F, F-22, F-35, etc. Aermet 310 steel with higher strength has lower fracture toughness and is currently under research. The crack propagation rate of the damage tolerant ultra-high strength steel AF1410 is extremely slow. When used as a joint for the B-1 aircraft wing actuator, it reduces weight by 10.6% compared to Ti-6Al-4V, improves processing performance by 60%, and reduces costs by 30.3%. The Russian MiG-1.42 uses up to 30% high-strength stainless steel. PH13-8Mo is the only high-strength martensitic precipitation hardening stainless steel widely used as a corrosion-resistant component. Preliminary results have been achieved in exploring ultra-high strength stainless steel domestically.
Ultra high strength gear (bearing) steel has also been developed abroad, such as CSS-42L, GearmetC69, etc., and has been tested in engines, helicopters, and aerospace. The technology of engine and helicopter transmission materials in China is very backward. Beijing Institute of Aeronautical Materials has independently researched and developed an ultra-high strength bearing gear steel.
05 Carbon/Carbon Composite Materials
C/C-based composite materials are the most highly regarded new materials with higher temperature resistance in recent years. So far, only C/C composite materials are considered the only successor materials for turbine rotor blades with a thrust to weight ratio of over 20 and an engine inlet temperature of 1930-2227 ℃. It is a key high-temperature resistant material developed by the United States in the 21st century and the highest goal pursued by advanced industrial countries in the world. C/C-based composite materials, also known as carbon fiber reinforced carbon basic composite materials, combine the refractory nature of carbon with the high strength and rigidity of carbon fibers, resulting in non brittle failure. Due to its lightweight, high strength, superior thermal stability, and excellent thermal conductivity, it is currently the most ideal high-temperature resistant material. Especially in high temperature environments of 1000-1300 ℃, its strength not only does not decrease, but also increases. It still maintains its strength and demeanor at room temperature below 1650 ℃. Therefore, C/C-based composite materials have great development prospects in the aerospace manufacturing industry.
The main problem with the application of C/C-based composite materials in aviation engines is poor oxidation resistance. In recent years, the United States has continuously solved this problem through a series of process measures and gradually applied it to new engines. For example, the tailpipe of the afterburner on the F119 engine in the United States, and the nozzle and combustion chamber on the F100 engine
Keywords: # alumina fiber # Dongheng national fiber # alumina continuous fiber # alumina fiber felt # alumina fiber felt # alumina fiber paper # refractory material # insulation material